In situ dynamic balancing
Correction of residual unbalancing as per standards, using the equipment itself as support through particular diagnostics and calculations techniques.
Unbalancing identification
Unbalancing is one of the common causes for vibration in rotating machinery. The capability to distinguish between unbalancing and other vibration causes is the first essential step in any balancing analysis or job.
Confirmation of unbalancing
There are various measurements that help determine when the main cause of the a vibration problem is unbalancing:
- Analysis of vibration spectra
- Wave shape
- 1X Phase
- Projecting rotors
Types of unbalancing as per ISO 1925 standard
- Static
- Dynamic imbalance
- Quasi -static
- Dynamic
ISO 1940/1 or VDI 2060 Standard.
This standard is valid only for rigid rotors. A rotor is considered as rigid if at its maximum service speed it does not rotate at a speed higher than its first critical speed. In practice a rotor is considered as rigid when its turning speed is lower than 0.5 or lower than 0.7 times its first critical speed.
Laser Alignment
Rolling bearings and parts, seals, and machine couplings life is closely related to the alignment condition of the equipment. To obtain the theoretical maximum useful life of every machine component, alignment is one of the maintenance practices that must be under strict control and with an accuracy degree to allow reaching these limits. In line with this, we propose to incorporate a machine laser alignment system (Fixtur Láser Sharp 50).
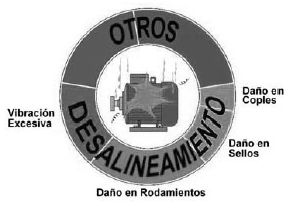
Advantages of laser alignment vs. mechanical alignment.
- Bars bending
- Hysteresis
- Low resolution, 1/100 mm
- Measurements errors
- Mechanical looseness
- Sloped indicator
- Axial looseness
|